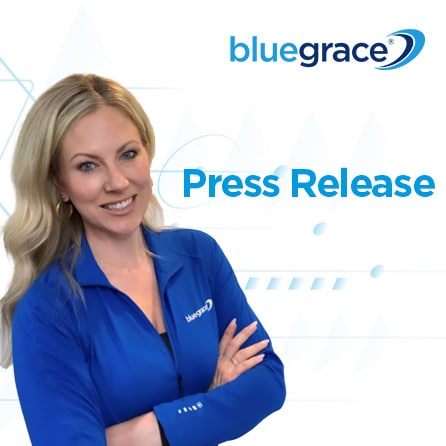
The COVID-19 pandemic caused a major upheaval in everyday life across nearly every industry. In freight, major supply disruptions have turned trucking on its head. An unprecedented demand on last-mile delivery quickly replaced initial slowdowns. Manufacturing continues to expand amidst labor shortages. Driver detentions exacerbate the current bottleneck issue at ports caused by empty containers being returned to Asia unfilled, due to demand flow. Normal operational conditions and the strategies used to manage them have gone out the window, with costly results. The good news is, those with an eye for innovation have an opportunity to jockey ahead of the competition.
COVID’s Costly Influence
Inflation is being driven by a combination of increased shipping costs and a quarantined labor force. Shipping demands are up. A rise in home-based e-commerce has resulted in a significant shift towards last-mile delivery. Freight has had to restructure its fleets to accommodate this, at no small expense to equipment and logistics planning. Containers are scarce, even at premium prices. Driver detention is up, conflicting with HOS regulations and requiring a larger workforce. Driver recruitment and retention are significant obstacles, which is in addition to the current driver shortage issue. The risk of infection has made in-person job training and travel less attractive. Shippers will have to offer competitive pay and incentives to sweeten the deal.
Too few hands on deck limit the growth potential of what could otherwise be a runaway manufacturing boom.
Additionally, many shippers responsible for distributing the COVID-19 vaccine require highly trained two-driver teams for one truckload, adding to the strain. Labor shortages in other professions are limiting growth as well. Short-term closures to sanitize facilities become less short-term on skeleton crews. Too few hands on deck limit the growth potential of what could otherwise be a runaway manufacturing boom.
Bottlenecks at ports occurred as a natural response to the shift from domestic in-person spending to shopping internationally online. Instead of buying from retailers who managed predictable inventories of imported goods, customers began making their orders with novel home-centered goals in mind. This profoundly disrupted trade patterns. The demand for imports, mostly from China to the US, has exasperated an existing imbalance in the flow of goods. China is not importing from US companies at nearly the same rate, causing a capacity nightmare. Sea freighters often choose not to wait for American exports to navigate congested ports and are sending back urgently needed empty containers.
However, with unpredictable route suspensions in response to COVID concerns, satisfactory results are mostly beyond the driver’s control.
Trucking companies are offering financial incentives to drivers who can pick up the pace to mollify the situation. However, with unpredictable route suspensions in response to COVID concerns, satisfactory results are mostly beyond the driver’s control. Companies that cannot afford to be affected by these delays are switching to expedited couriers. This can be an added cost for companies who choose to outsource in this way and also for companies who lose business to couriers.
Evading Expensive Pandemic Pitfalls
COVID-19 has changed the landscape of the freight industry. Knowing this, and knowing what to do about it, however, are two very different things. While the vaccine roll-out is fantastic news, it will still be quite some time before things get back to normal. Here are some things to keep in mind as we navigate our way through another year of COVID-19.
Optimize Labor Configuration
- Mitigate the risk of shut-down due to the spread of illness among employees by following WHO guidelines and protocols
- Evaluate how policy changes abroad could affect your business, suppliers, and trading partners
- Address continuity by creating contingencies for the loss of key players within your business, through distribution channels, and among suppliers
Prioritize Transparency
- Set up a command center for integrated and instant communication across all channels.
- Redirect resources in a dynamic and unprecedented environment.
- Quickly identify and respond to influences that threaten the supply chain.
- Consider upgrading ERP systems and building well-integrated KPIs.
Risk Management
- Establish proactive strategies that factor in supply chain disruptions and detect early signs of trouble.
- Consider a granular, high-resolution digital twin. According to Forbes, “Supply chain planning is done for different forecast horizons – factory scheduling and fulfillment planning may be focused on what will be made and delivered in the next week. This is known as operational planning. Tactical planning is focused on what will be made and delivered in the next month or next few months. Strategic planning is focused on even longer time horizons – plans going out many months or even years.”
Fortify Supplier Relationships
- Investigate suppliers within the supply chain to lower risk.
- Gain insight into potential obstacles with the suppliers’ region, culture, political atmosphere, restrictions, etc.,
- Protect shareholder interests with ethical choices.
- Reduce the potential for losses by formulating a response to many possible scenarios.
- Have backup suppliers lined up and integrated into contingency plans.
Restructuring logistics while maintaining operations is a challenge even within existing business models. Doing so while the world reinvents itself is a shot in the dark. Shippers will need to follow the example of thoroughly integrated giants like Amazon to survive. High-resolution 3PL support promises to pay for itself in salvaged opportunities moving forward into this gripping new landscape.