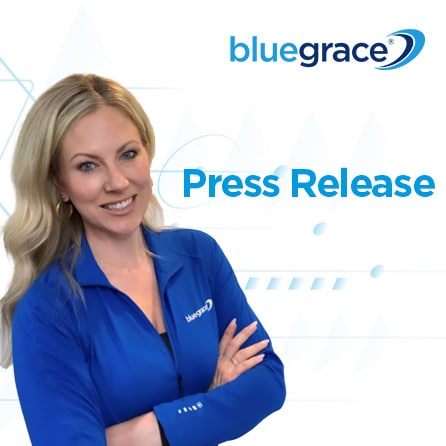
Inventory is the core of any business. The right inventory, at the right time, at the right point in the supply chain is crucial for the success of the business.
For example, the shortage of raw material at the factory will affect production. If warehouses are not replenished on time, distribution will be derailed. If retail outlets run out of stock, sales and customer relationships will be adversely impacted. Each of these processes in the supply chain is dependent on the availability of inventory to carry out their function and meet business objectives.
While the unavailability of inventory results in a loss of sales, too much inventory leads to an increase in the carrying cost.
While the unavailability of inventory results in a loss of sales, too much inventory leads to an increase in the carrying cost. Carrying cost is the cost incurred to store, handle, and maintain inventory at every stage in the supply chain.
The factory, warehouse, and the retail outlet all incur the cost of storing and managing the inventory until it is required at the next stage in the cycle or sold. A high carrying cost ultimately impacts the price of the product and the profit margins of the company. Hence, neither excess nor a shortage of inventory is an ideal situation.
This is why it is essential to understand the inventory consumption pattern and arrive at an optimum level that needs to be maintained at each stage in the supply chain.
Why does the State of the Supply Chain matter?
How you operate your supply chain, how agile it is, the technology you use, the level of digitization, the extent of integration among the different stages of the supply chain. All these things affect the performance of the supply chain. The level of inventory you need to maintain at all times is dependent on the capability of these parameters.
An agile, integrated, and digital supply chain makes it easier to understand how the inventory is being consumed at each stage.
An agile, integrated, and digital supply chain makes it easier to understand how the inventory is being consumed at each stage. It enables inventory managers to calculate the optimum level of inventory more accurately. The optimum level of inventory is where minimum carrying cost is incurred and there is no loss of sale or disruption in the production or delivery process. In other words, the inventory reaches the required point just in time – not any sooner, and not later.
When organizations use this strategy to design their supply chain they inevitably improve their inventory management.
Winning Logistics Strategies in the Race to the Urban Consumer, a whitepaper by DHL and Euromonitor on last-mile transportation, explained how companies can become more competitive and improve their supply chain by adopting the F.A.D strategy. The F stands for flexible transport, A is automation, and D is data management. When organizations use this strategy to design their supply chain they inevitably improve their inventory management. They can better plan inventory inward and outward movements, improve on speed and reduce administration and handling costs, can improve inventory forecasting and planning, process data real-time, and provide shipment tracking.
For example, this article cites how Apple understood the importance of supply chain management as early as 1997 and with proper supply chain planning, the company successfully managed to beat the competition. For the Christmas of 1998, the company bested its competition by simply changing its freight mode from sea to air.
“To ensure that the company’s new, translucent blue iMacs would be widely available at Christmas the following year, Jobs paid $50 million to buy up all the available holiday air freight space, says John Martin, a logistics executive who worked with Jobs to arrange the flights.”
This one change made sure that its products were easily available during the holiday shopping season. Apple could not have done this if it had followed a rigid approach to transport planning and management.
And, if the delighted customer is also a competitor, you know you’re doing something right.
Another example in the article shows how it delighted customers with quick delivery and shipment tracking. And, if the delighted customer is also a competitor, you know you’re doing something right.
“When iPod sales took off in 2001, Apple realized it could pack so many of the diminutive music players on planes that it became economical to ship them directly from Chinese factories to consumers’ doors. When an HP staffer bought one and received it a few days later, tracking its progress around the world through Apple’s website, “It was an ‘Oh s—’ moment,” recalls [former HP supply chain chief Mike] Fawkes.”
What are the benefits of a well-managed supply chain?
A supply chain that is managed properly makes it easier to monitor stock at various touch points. It can help improve inventory forecasting and distribution. Some of the benefits that such a supply chain offers for inventory management are:
Visibility: Visibility allows inventory managers to monitor inventory levels at each stage. With a continuous and real-time view of the inventory, they can place orders or plan distribution of the inventory to reach the intended destination on time.
A strong transportation management system also enables you to store historical data, provide advanced analytic tools and trend reports, enable users to optimize freight expenses thus helping you create an efficient shipping process.
TMS: While inventory is the life of the business, transportation is the backbone. Without adequate transportation management, it will be challenging to get the inventory to the right place at the right time in the required condition. In addition to planning transportation, a strong transportation management system also enables you to store historical data, provide advanced analytic tools and trend reports, enable users to optimize freight expenses thus helping you create an efficient shipping process.
Integration: We cannot stress this enough. Integration is crucial to get complete control over inventory. For integration to be truly successful, it needs to take into account the needs of different departments and their workflow. When all the parties handling inventory are able to connect to the same system, only then will you be able to get better visibility of your inventory, improve tracking, and planning.
Analytics: The digital supply chain is a substantial resource of hard data. It provides stakeholders with the opportunity of developing and monitoring KPIs and assist them in improving their supply chains. When the data for all the functions are gathered at a single reliable source it increases accuracy in forecasting and improves execution. The reports and trends can be used for making informed decisions.
The state of your supply chain and inventory, the levels you need to maintain are directly related. If the supply chain is equipped with the latest technology and is functioning at optimal levels at each stage, it would reflect in the form of optimum inventory levels. If it is not, then you may see piles of inventory accumulated at each stage. There may be situations when you need to keep unusually high or low inventory levels. However, when inventory levels fall below or go above the optimum without a valid reason, take it as a red flag, talk with an expert. Contact us at 800.MY.SHIPPING or fill out the form below to connect with our team today for a FREE analysis of your supply chain.